Simply blue
New material concept allows more cost-effective production of blue organic light-emitting diodes
Blue organic light-emitting diodes (OLEDs), which can be used in smartphones, televisions or other devices, are still difficult to manufacture today. A team of researchers led by Gert-Jan Wetzelaer of the Max Planck Institute for Polymer Research has now developed a new material concept that allows blue OLEDs to be manufactured easily and cost-effectively. The efficiency of the developed light-emitting diode is already comparable to commercially available ones that employ a far more complex structure.
Red, green and blue: the three primary colors are used in all kinds of modern displays to show colored images. In current screens that use organic light-emitting diodes (OLEDs), one pixel consists of three individual, microscopic OLEDs. An entire television screen with approximately 2 million individual pixels thus consists of 6 million light-emitting diodes. Therefore, ease of manufacture as well as high energy efficiency is of high importance for both manufacturing costs and subsequent electricity costs.
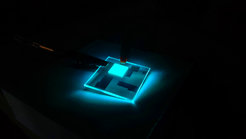
So far, the production of blue organic light-emitting diodes has been a challenge. To obtain a high efficiency , modern organic light-emitting diodes use a multilayer material system. This sandwich structure, sometimes comprising up to seven layers, allows efficiencies of light emitted to the outside between 20% and 30% to be achieved.
Researchers led by Gert-Jan Wetzelaer, group leader in Paul Blom's department at the MPI for Polymer Research, have now developed a much simpler OLED structure. They were able to show that instead of seven layers only a single active layer, which is responsible for light emission, between two contacts is already sufficient to obtain an efficient organic light-emitting diode. A key ingredient of the material used in this single layer is the prevention of detrimental effect by defects as water and oxygen.
"With our material system, efficient blue OLEDs could also be produced from solution in the future," says Gert-Jan Wetzelaer. "This means that manufacturing then no longer involves a multi-step process and complex evaporation equipment, but such OLEDs can also be printed in the best-case scenario."
With their new single layer OLED concept, they were able to achieve an internal quantum efficiency of 100% - meaning that the complete electrical energy supplied is converted into light. Due to optical losses at interfaces, which are present in every OLED, about 27% of the light is emitted to the outside - a value that is competitive with the existing complex commercial OLEDs.
The scientists have now published their results in the renowned journal "Advanced Materials".